Gap Measurements in Wind Turbines Applications
Rotor to stator gap measurement:
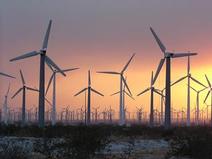
On-Line
Miniature non contact displacement sensors along with high frequency compact electronics are installed in Wind Turbines to measure the electric generator's rotor to stator gap on a real time basis. Out of spec measurments are fed to a central wind turbine monitoring station allowing utlitites to constantly monitor this critical dimension. This helps wind farms to better plan maintenance, reduce unexpected off grid time and per-kWh operating costs.
During Assembly
As a more precise and repeatable method, Gapman "an electronic feeler gage" is used instead of feeler gages to set the gap between the rotor poles and the stator. This gap is particularly critical at the 6 o'clock position due to the gravity effect of the heavy rotor shaft and magnetic assemblies. In a 1.65 kW model 50 to 60 individual pole gaps must be measured.
Additional Applications
-
Gap measurement between cogwheel teeth in pitch control and other actuators: Control the gap distances of approx. 0.5mm to 1.5mm between the actuator teeth and the cogwheel using the Gapman with a special 0.4mm thickness dual sensor wand.
-
Emergency Disc brake rotor to brake pad gap set up: In this application the gap must be set between the non-conductive brake pad and the brake disc. Capacitec "spring contact wand" is used in conjunction to measure these larger gaps up to 5mm.
-
Nacelle to tower parallelism: Gapman can also be used to set the parallelism between the nacelle and tower platform by measuring and setting gaps around
the circumference. -
Other Applications:
• Condition Monitoring System with real time measurement of rotor stator gap during operation to prevent catastrophic failures.
• All other critical gap, parallelism or hole measurements during the manufacturing and final assembly.
• Sensors for maintenance tools for generator, gearbox, rotor hub, …